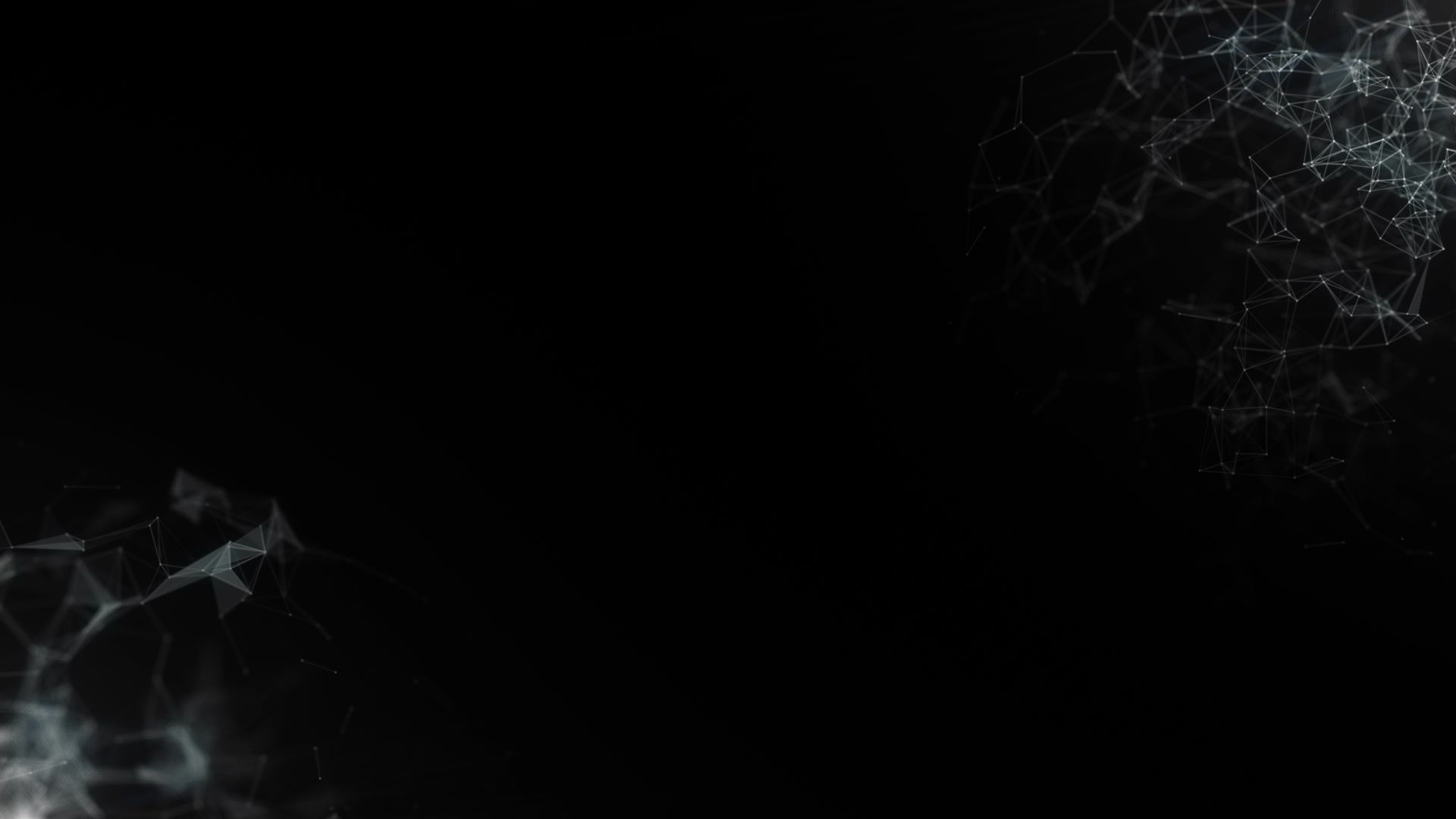
SDSu Mechatronics
MOSFET Steady-State and Transient Thermal Analysis
In Mechatronics at San Diego State University, myself and one other member were assigned the task of running a thermal analysis on a MOSFET inside the submarine using SolidWorks Thermal Simulation. The objective of this assignment was to ensure that air inside the submarine did not overheat via the MOSFET and that the MOSFET itself did not overheat. We began by calculating the total heat power of the MOSFET when each of the four thrusters on the vehicle are operating at maximum rotational speeds. At maximum rotational speed each thruster takes in 350 W, for a total 1400 W coming into the MOSFET. However, since the thrusters are 95% efficient, only 70 W of heat is being generated by the MOSFET. The bottom of the hull, where the MOSFET sits, is 6061 Aluminum and it functioned as a heat sink in this system. The 70 W of heat power, a convection coefficient of 50 W/(m^2.K) between the water and the bottom of the submarine, and a bulk ambient temperature of 298 K, served as the inputs for thermal loads in the SolidWorks Thermal Simulation. After adding the appropriate connections, we ran four steady-state simulations, slightly adjusting inputs in each, to collect a reliable set of data. The results can be seen in the documentation below.